Pro/TOOLKIT与VC++的减速器参数化设计系统二次开发
以直齿圆柱齿轮二级减速器为研究对象,在Pro/E平台上通过“自下而上”的模式建立其模型样板。在Visual Studio 2008编译环境下,以Pro/TOOLKIT和Visual C++9.0作为二次开发工具,创建了各主要零部件的参数化设计对话框,在此基础上,采用动态链接库方式成功开发出了基于Pro/E的人机交互主界面,增强了减速器产品设计的灵活性,为减速器参数化通用设计平台的实现奠定了基础。
引言
随着CAD/CAE/CAM技术的飞速发展,三维造型、参数化设计和虚拟现实技术等新概念、新方法已渗透到工程设计领域,使传统的结构设计模式正在发生深刻变化。减速器是一种典型的传动装置,在机械、汽车、电子、航空航天等领域被广泛应用。减速器结构复杂,研发过程涉及多个零部件的设计、制造及装配,传统方法只是一种针对固定结构尺寸的单一设计模式,一旦涉及到减速器的结构改进或产品改型,这种固有的设计模式不仅会大量地增加成本和人工,而且不能在较短时间内响应市场要求,在一定程度上制约了企业利润的增长。为了使减速器的设计更具灵活性,更好的适应产品改型及市场要求,本文以Pro/E提供的二次开发工具Pro/TOOLKIT为平台,在Visual C++环境下进行编程,成功开发出了一套基于Pro/E的减速器参数化设计人机交互界面。
1、参数化设计基本思路
参数化设计是一种使用几何参数快速构建和修改产品结构模型的方法。通过参数化设计技术,只要改变一个或多个重要参数就可以实现模型的更改和重建,与传统设计方法相比,参数化设计最大的不同在于存储了整个设计过程,能设计出一族而不是单一的产品模型。
Pro/E最早提出的全参数化设计(单一数据库)理念一直沿用至今,同时也被多款三维设计软件所借鉴,如UG、SolidWorks等。Pro/E具有十分强大的参数化设计功能,其主要特点是全数据相关、尺寸驱动设计修改、全尺寸约束。对于单一零件实体,可通过修改一个或多个设计参数来实现模型的驱动;对于由多个零部件组成的机械系统,可通过设立关系式及编写程序对其进行参数控制,从而实现对于装配体的参数化设计。
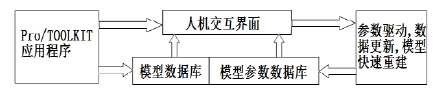
图1 参数化设计基本原理
如图1所示,Pro/E参数化设计的基本原理是采用三维模型与程序控制相结合的方式,在已有零件三维模型(原始模型)基础上,根据设计要求建立一组可以完全控制零件实体形状及几何尺寸的设计参数,同时建立模型参数数据库,并在Relation命令下定义各参数的约束关系。模型的重建不是由程序控制的,而是通过人机交互方式生成。利用Pro/E提供的用户化工具箱Pro/TOOLKIT开发出可视化用户界面,然后参数化程序对模型的设计参数进行编程,通过交互对话框实现模型数据的检索、修改和更新,最后生成新的模型。
2、二次开发流程
2.1、参数化设计的实现
要实现模型的参数化驱动,首先必须建立一个模型样板,对其设置合理的参数,并对这些参数进行命名和初始赋值,通过正确分析模型各参数之间的关联性来定义参数驱动关系,最后存模型作为参数化设计系统的原始模型。直齿圆柱齿轮二级减速器包含多个零部件,限于篇幅,本文仅以高速齿轮轴为例,对其参数化设计基本过程及交互界面的二次开发进行介绍。高速齿轮轴由轴和齿轮两部分构成,其模型样板如图2所示。
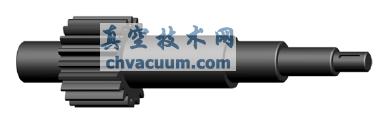
图2 高速齿轮轴模型样板
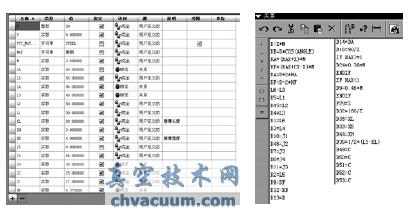
图3 【参数】与【关系】选项
对于轴的参数化设计主要包括各轴段的长度L、直径D、以及其他相关的特征参数,参数之间的相互约束关系是模型参数化驱动的依据。对于轴上齿轮的参数化设计,需分析多个结构参数之间的关系,包括:齿数、模数、压力角、分度圆直径、基圆直径、齿顶圆直径、齿根圆直径、齿顶高系数、顶隙系数和齿宽等,根据这些参数之间的关系来区分设计模型的主动驱动参数和从动驱动参数。齿轮轴的模型样板建立完成后,通过Pro/E的参数选项对其设置约束参数并赋予初值,主动驱动参数设定为在交互界面上需要输入的参数,从动驱动参数与主动驱动参数之间的约束可通过关系选项来定义,如图3所示。
2.2、交互界面二次开发
选用Visual Studio 2008为编译平台,通过Pro/TOOLKIT与Visual C++9.0开发齿轮轴的交互界面。Visual Studio 2008是目前最流行的Windows平台应用程序开发环境,可以用它来开发多种Windows下的软件项目[6]。Pro/TOOLKIT模块有两种工作模式:同步模式和异步模式。由于异步模式代码复杂、执行速度慢,所以本文采用同步模式进行二次开发设计。在同步模式下,Pro/TOOLKIT必须与Pro/E系统同步运行,同步模式又包含两种运行模式:动态链接模式(DLL Mode)与多进程模式(Multiprocess Mode)。动态链接模式是将用户编写的C程序编译成一个DLL文件,使Pro/TOOLKIT和Pro/E在同一进程中运行,通过直接调用函数实现信息交换。多进程模式是将用户的C程序编译成一个可执行文件,Pro/TOOLKIT和Pro/E运行在各自的进程中,两者之间的信息交换是由消息系统来完成的。由于DLL模式的运行度快,函数调用及信息交换方便,因此本文选用同步模式下的动态链接模式。
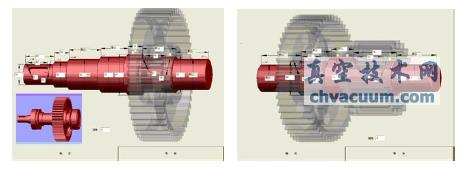
图4 参数化设计交互界面
低速轴及中间轴的交互界面如图4所示,每个组合框控件都可以在定义范围内输入不同的数值,从而控制轴和齿轮的结构参数,如齿数、模数、轴段长度和直径等,参数设置完成后点“确定”按钮就可更新数据,生成新的齿轮轴模型。
3、人机交互主界面
完成各主要零部件的参数化设计及交互界面设计后,可将其集成到一个主界面上统一管理。本文采用“自下而上(Down-Top Design)”的设计模式,首先建立减速器各主要零部件的参数化模型,实现单个零部件的参数化尺寸驱动,在此基础上对其进行装配设计,装配完成的减速器整机模型如图5所示。建模过程考虑了标准齿轮的正确啮合条件及连续传动条件,由此保证了各零部件参数改变后减速器的传动关系及装配关系随之更新,避免了模型在重建时发生干涉及碰撞。
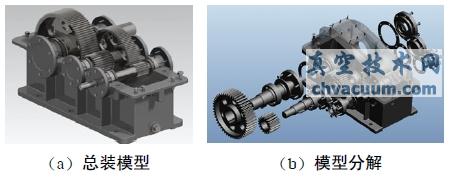
图5 减速器整机模型(Pro/E环境下)
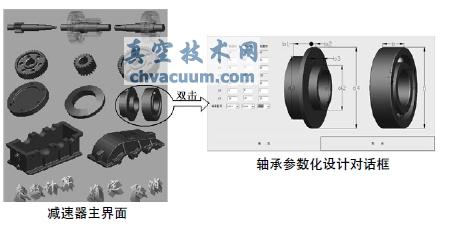
图6 减速器参数化设计系统主界面
开发完成的减速器参数化设计系统主界面如图6所示,共包括11个主要零部件:低速齿轮轴、中间轴、高速轴、传动齿轮(3个)、端盖、密封圈、轴承、箱体座和箱体盖,各零部件之间通过单一数据库相互关联。当要更改减速器某个零部件的结构参数时,只需双击主界面上的位图按钮就会弹出相应的参数化设计对话框,例如图6中的标准件轴承,双击打开轴承参数化设计对话框,对于高速轴、中间轴及低速轴可选择不同的轴承型号,每个型号的径向尺寸d1、d2、d3、d4及轴向尺寸b1、b2、b3均不相同,点确定后Pro/E系统会自动更新数据库重建轴承模型,与此同时减速器系统也会自动更改与轴承参数相关联的结构尺寸,如轴颈、密封圈及箱体壁上的孔直径等。其余10个零部件也具有类似的参数化设计与关联性设计功能,鉴于篇幅不再熬述。通过人机交互主界面可以方便、快捷地对减速器多个结构参数进行同步修改,大大提高了工作效率与设计质量,为减速器的系列化设计与结构改进提供了支持,同时也为同类产品的参数化设计系统二次开发积累了经验。
4、结束语
本文将Pro/E的参数化技术应用于减速器设计,通过Pro/TOOLKIT工具箱与Visual C++9.0编译平台实现了减速器参数化设计系统的二次开发,成功创建了基于Pro/E的人机交互主界面,简化了减速器的设计流程,可方便、快捷的设计出用户所要求的减速器类型,大大减少了重复性设计工作。本系统运行稳定,可满足减速器零件库快速建模及产品系列化设计要求,为减速器参数化通用设计平台的实现奠定了基础。同时,对其他机械产品的参数化设计与通用平台开发提供了技术参考。