泵送系统整体节能方法
泵送系统占全球电能需求的将近20%,在某些工厂中,它们所消耗的电能可以占到整个工厂用电量的20%-25%。在加工、发电、水务和建筑行业中,离心泵是主要的耗能设备。建筑和工厂是能效关注的重点,因为它们几乎占全球用电量的80%。尽管如此,泵送设备却很少被业内人士视为潜在的节能对象。
使泵运转的能源成本被业界视为不可压缩的费用,通常将其归入固定成本。但是,通过使用一种系统方法可以将能耗降低20%-80%,从而使其变成了一项可变成本。
对英国已经安装在用的设备进行审核,每年可以节省逾10 TWh的电能,减少大约550万吨的CO2排放量。
安装高效的泵和电机只能节省很少的能源。为了提高整体效率,必须考虑整个泵送系统(如图1所示)。
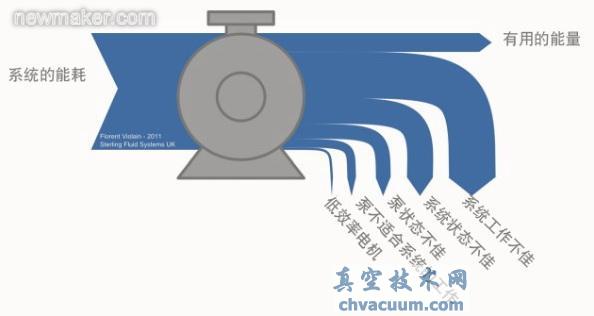
应用系统方法来达到节能的目的,在某种程度上类似于‘精益制造’。从根本上来说,只有在必要的时候、必要的地点才泵送流体,这符合‘准时化’的原则。该方法旨在消除不必要的工序,从而使工艺得到显著改进。
在评估已经安装的设备时,能效是重点审核内容;它是实现整体系统节能的重要环节。到目前为止,能源费用是泵的寿命周期成本中花费最大的一部分(图2)。根据泵的类型和运转状态,其能源费用占泵寿命周期成本中的40%-90%之多。此外,系统的工作效率不高还会导致能量转化为有害的热能和振动。
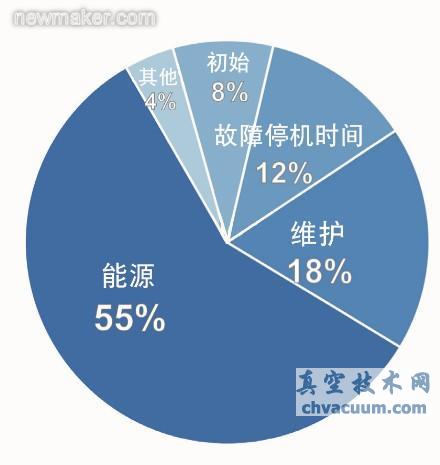
这会对系统零部件的可靠性造成不良影响。泵的实际工作点离最佳效率点越远,其平均无故障工作时间就越短。因此,我们可以得出以下结论,即节能有利于减少维护和故障停机的时间成本。
泵送系统是工艺过程的关键设备。当它发生故障时,所造成的经济损失往往远远超过了其修理成本。国际纸业公司(International Paper)经营着全美国的所有造纸厂。在为期一年的观察中,发现它们经历了101次泵故障,总共造成高达500万美元的生产损失。每次故障的平均花费为5万美元,其中相当大一部分是由于工厂停工造成的经济损失。最严重的泵送设施故障案例之一是2011年海啸引起的福岛第一核电站故障。当冷却装置被水淹之后,泵送系统发生故障,进而造成三个受损的核反应堆发出巨大的核辐射。
整体系统节能
系统理论根据系统与外部世界的边界和界面来定义系统(假设它是开放的系统)。在大多数情况下,泵送系统是开放的,而且通常相当复杂。因此,必须清楚地了解系统的边界,以及输出、输入的动态变化。使用一副简单的草图即可清晰地说明泵送系统的主要特点。
评估泵送设备的能耗需要适当的方法和工具。泵送系统用能量评估标准ASME EA-2-2009中提供了合适的指导方法。此外,由美国能源部组织的泵送系统评估工具(PSAT)培训可以提供必要的技能和知识。
遵循以下步骤即可便捷地对泵送设备进行评估:
A.确定泵送系统当前的工作任务。
B. 确定实际需求。
C. 调研主要的能量损失点在哪儿。
D. 采取相应的措施减少能量损失。
E. 使供给(泵和系统)与需求(工艺)相匹配。
F. 控制所采取的改进措施的有效性。
泵的性能
通常用一条性能曲线来表示泵的液压特性,用一条系统曲线来表示整个泵送系统的工作性能。这两条曲线都是利用扬程与流量的比率关系绘制而成的。工作点表示泵的液压条件,该点位于两条曲线的相交处。泵与系统协同工作,系统起主导作用,同时要遵循泵提出的限制条件。
不同类型的泵的性能曲线各不相同,具体取决于转速。系统曲线体现了本质特性(例如提升高度、管道损失等)与工作变量(例如调节阀、液位等)的综合作用。
泵与系统曲线是利用评估期间的现场测量数据来计算的,这些数据准确地反映了典型工况。评估大体上是一个无干扰过程,几乎不干扰工艺。因为泵送系统几乎没有处于静态状态的,因此必须确定工作变量。认识系统和泵的特性有利于找到能量损失的源头,并确定可能从哪些方面采取相应的节能措施。
寻找能量损失的源头
低效能的源头是评估泵送系统时关注的重要问题。有些源头显而易见,但是还有不少源头乍看之下难以发现。通常泵送设备看起来一切正常,运转良好,但是实际上浪费了大量的能源。
许多能量损失都与设备的历史有关,例如,修改、技术选择、使用了过高的安全余量等等。各种故障现象相互关联,难以区分彼此,从而导致难以找到问题的根源,无法确定故障后果的严重程度。
能量浪费源头的一些例子:
•管道和配件内的摩擦损失——这是最普遍的低效能的根源,它与液流在管道和配件内的流速有着直接的关系。选择合适的泵规格能够节省大量的能源。此外,洁净的管道和流线型的布局也有利于节能。
•泵不适合系统——泵没有工作在其最佳效率点,从而导致可靠性问题,并且浪费能源。这通常发生在为新厂房选择泵的阶段。由于管道系统模拟无法给出“准确的”信息,导致选用了规格过大的泵,所以使得系统的安全余量过高。为了降低成本而购买接近其最大工作流量的泵也会导致同样的问题。此外,如果由于工艺发生变化而对系统的特性参数进行了修改,却没有对泵做任何改变(例如调整叶轮或者更换泵),那么也会导致泵与系统不匹配。
•阀门节流和调节阀——当使用调节阀时无可避免地会出现低效能问题,因为它们依靠摩擦损失来调节流速。节流的数量意味着能量损失的多少,还说明泵的规格过大(参阅3.1节实际案例)。
•不必要的静压头——提升流体所需的能量不一定总是有用,静压头有时过大。例如,排水箱液位高而入水箱液位低,这是一种常见的问题。另一个例子是用露天排放管道取代止回阀。
•旁路/回流——尽管有各种理由使用旁路系统,但是它们的确是浪费能源的主要源头。在这种情况下,有一部分液流在经过泵送之后返回吸入侧,未被实际工作利用。通常安装旁路是为了避免在某个工序不用时关闭泵,从而将我们带到下一个工作点。
•当工序不用时管道内仍有流体流动——当液流在管道内不必要地流动时,系统消耗的能量是无效的。例如,常常发现冷却水在不工作时仍然流向环路和换热器中(参阅3.2节的实际案例)。
•供给大于需求——这是能量浪费的最大源头之一,却常常被人们忽视。当液流的流速超过工艺的需要时,或者当泵在不需要工作的情况下仍保持运转时,都会造成能源的浪费。和某些输送应用一样,闭环系统常常以这种方式工作。当供给并非由需求来驱动时,还会造成其他的能量损失,例如本文前面所提及的那些。
能量浪费的源头往往相互关联,这意味着它们造成的后果会重复发生。所以,减少每一种源头都有利于加强最终的节能效果。达到该目的的最直接办法就是针对工作任务选择合适的泵,并调整流量。
工艺需求
只有使泵送设备在需要的时候(准时)提供需要的功能,才能实现节能的目的。这意味着要确定泵的真正用途,在大多数情况下它并不是为了输送液流。例如,在过滤管道中安装的泵可用于辅助清洁液流;但是它的最终功能取决于为什么要首先清洁液流。“五个为什么”的方法有助于我们理解系统的目的。例如,当考虑结晶过程中所用的冷却水泵时:
问:为什么系统中安装有泵?
答:为了输送冷却水。
问:为什么要输送冷却水?
答:为了加速散热。
问:为什么要加速散热?
答:为了在规定的时间内使工艺冷却。
问:为什么需要在规定的时间内使工艺冷却。
答:为了控制结晶速度。
问:为什么需要控制结晶速度?
答:为了获得合适的晶体大小。
结论:泵的工作任务由晶体大小来控制。
如果当泵运转在最低流量工况下,仍然能确保实现系统的最终功能,那么就能达到最佳效率。液流在管道内的流速与流量成正比。摩擦损失随流速的平方变化,因此会随流量的平方值而变化。所以,减小流量有利于提高比能——使系统中单位体积的流体移动所消耗的能量。最后,为了达到期望的性能,应保证泵组适合其工作任务。
当需求变动时,系统的工作条件也相应地发生变化。确定系统在一段时期内的载荷情况有助于了解泵送设备的工作任务(图7)。为了确定泵的工作模式,需要首先确定主要的工作点,这意味着能够通过变化的工作负载计算出可能的节能量(这不同于使用单一的固定工作点)。
工艺需求取决于合适的泵送系统的工作情况。了解工艺的动态特性和需求对于确定工作方式起着重要作用。
固定的需求:
恰当的操作取决于泵的选择和系统布局。选择一台能够在其最佳效率点提供所需流量的泵是目标所在。扬程值由泵送设备在指定流量下的规定值来确定。PAST软件能够计算出当泵送系统工作在指定工作点时的泵和电机效率。当弄清楚工作任务和系统布局之后,就能提高该阶段工作的成效。
变动的需求:
如果需求波动,那么泵送设备就必须运转在多个工作点下,并且必须恰当地处理中间状态。妥善的解决方案取决于系统的特性参数(例如静压头、摩擦损失)和工作点。在一切可能的情况下,都应该尽量使需求的变动平稳、简化,例如通过使用缓冲罐来达到这一目的。这样做能够降低峰值流量,从而减少能耗。
如果波动方式复杂,系统的操作会变得困难,往往需要一台或者多台泵以及特定的控制方法。常见的调节方法依靠调节阀和旁路。但是,现代控制技术避免使用低效能的元件,因为它们是以传感器和计算信息作为反馈环节的控制环路为基础的。它们通常更接近所要求的工作任务,而且更复杂。
使用变速驱动器能够解决需求变动的问题。但是,它并非一种普遍适用的解决方案。务必要了解在何处以及如何使用变速驱动器,这一点相当重要,因为如果使用不当,则会导致能耗增加而无法节能。
对方案进行优化时要考虑实际工作中的重点和限制。往往不止有一种解决方案,因此可有多种方法来实现投资回报。节能效果最优的并不是节能潜力最大的解决方案,而是可实施性最好的方案。必须将能量审核的结果付诸实践,以达到节能的目的,只有这样才能使减少的能耗量,将缩减的维护和故障停机时间成本转化为经济效益,从而帮助实现预期的投资收益。
实际案例
英国进行了许多整体系统节能评估,下面介绍了加工行业中的两个案例。二者都针对工作在现场的数百套泵送系统之一进行节能评估。
加工车间,食品行业,伦敦
*工作任务:将工艺流体从机械过滤器输送到供应罐。
*泵:两台具有开式叶轮的离心渣浆泵,二者交替工作。传送带由110 kW的电机驱动。
*年耗电量:590 MWh,41,300英镑,电价为0.07英镑/kWh。
* 能量损失的主要原因:用于调整流量的调节阀仅工作在10%到40%的开度范围内。显然泵的规格过大,调节阀浪费了过多的能量。
*解决方案:减小泵的规格,并用变频驱动器(该设备适用于泵的更新)取代调节阀。
*结果:节省了高达93%的能源,每年的电力成本缩减了44,000英镑(单价8英镑 /kWh)。二氧化碳排放量减少了298吨。
加工车间,制药行业,苏格兰
*工作任务:冷却塔和几个流程之间的冷却水回路。
*泵:两台具有闭式叶轮的标准离心泵,二者交替工作。与75 kW的电机相连。
*年用电量:370 MWh,25,900英镑,电价0.07英镑/kWh。
*能量损失的主要原因:确定冷却设备的规格时,工作现场的面积比较大,而且考虑了今后扩容的需求。但是现在的需求降低了不少,入口和出口的温差很小。
这说明流量过高,泵的规格过大。此外,冷却水在换热器和不用的流程管道内流动。缺乏合适的控制方法来改变系统的工作负载,同时隔离不用的管道。
*解决方案:减小泵的规格,并安装一台变频驱动器,利用入口和出口的温差来调节流量,然后采取常规程序隔离不用的管道。
*结果:节省了多达86%的能量,每年的电力成本缩减了20,000英镑。二氧化碳排放量减少了172吨。
结论
采取系统方法能够提高能效,减小维护和故障停机时间成本,从而降低泵送设备的生命周期成本。评估得出了定量的潜在节能数据,并提供了实践指导,尤其强调了有效的解决方案和可能的投资收益。现在可以对那些相比于从前发生变化的工艺予以改进,提高它们的效率,使工艺的投资回报时间变短,最终使系统变得更加灵活,更加适应实际工况的需要。
泵送系统在许多工艺中都是非常关键的设施。增强它们的性能有助于缩减工厂的故障停工时间,降低工作成本,同时提高灵活性。工业行业正面临着成本高涨和不确定性因素增多的问题,因此,同时提高最终效益和生产率对大部分工厂来说都是一个好消息。
是否能达到期望的节能效果取决于评估的质量。因此,评估团队的技能和所用的方法非常重要。公认的资格和认证有助于增加泵用户对该项服务的信心。但是,目前针对泵送系统进行评估的认证机构和审核人员并不多见——这还是一个尚在发展的新兴领域。尽管如此,美国能源部和英国泵业制造商协会所做的一些工作表明了今后的发展方向。