超临界600MW机组主汽阀阀杆断裂原因分析
采用宏观形貌观察、化学成分分析、显微组织观察与力学性能试验等方法,对某超临界600MW机组主汽阀阀杆断裂原因进行了分析。结果表明,该高温合金阀杆母材弥散分布富Al、富Si、富Ti和富Mo的强化颗粒,显微组织异常,且拉伸塑性与冲击韧性较差,是导致其在丝扣退刀槽处发生脆性断裂的主要原因。建议对同批次和同类型的主汽阀阀杆采取适当的措施进行处理,确保机组安全运行。
1、阀杆断裂情况
某超临界600MW机组于2010年10月12日7时并入系统运行,8时发现调节阀全开后,机组仅能带370MW负荷。进一步检查后发现,左、右侧主汽阀体温差大,右侧主汽阀处无明显节流声,判断其阀芯没有开启。2010年10月18日,对右侧主汽阀进行解体检查,发现该阀阀杆与阀杆套筒连接丝扣断裂。
主汽阀材质为GH901铁基高温合金,该合金在650℃以下具有较高的屈服强度和持久强度,760℃以下抗氧化性良好,长期使用组织稳定,是一种较成熟的合金,广泛用于制造在650℃以下工作的航空及地面燃气涡轮发动机的转动盘形件、静结构件、涡轮外环及紧固件等零部件,同时也用于超临界发电机组的主汽阀阀杆。
沿主汽阀阀杆轴向切割规格为12.5mm×5mm×160mm的拉伸试样和规格为5mm×10mm×50mm的V型缺口冲击试样,拉伸试验在UTM5105型万能材料试验机上进行,拉伸速率为2mm/min;冲击试验设备为JBN-300。
2、宏观检测
主汽阀阀杆上部断口形貌如图1所示。主汽阀阀杆在其上部丝扣的退刀槽处发生断裂,断口无明显的塑性变形,是典型的脆性断裂,且断面无疲劳特征,因此可以排除疲劳断裂的可能。
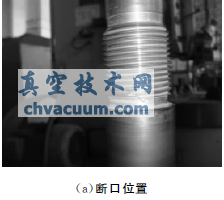
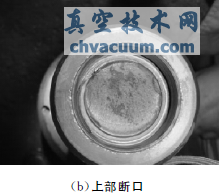
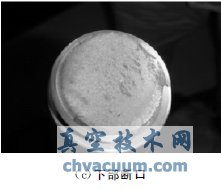
图1 主汽阀阀杆断口形貌
3、成分分析
GH901合金中的Fe是基体元素,Ni是奥氏体稳定化元素,Cr是抗氧化腐蚀元素,B为微量晶间强化元素,钛、铝等为时效强化元素,其中Al还可抑制合金中主要强化γ"相向脆性η-Ni3Ti相转化。主汽阀阀杆的合金成分见表1,各化学元素含量符合《中国航空材料手册》(以下简称“手册”)要求。
表1 主汽阀阀杆元素含量 at%

4、显微组织
在主汽阀阀杆断口位置附近取样进行金相试验,其组织为奥氏体,但内含异常的混晶组织,不符合DL/T439-2006《火力发电厂高温紧固件技术导则》中关于奥氏体组织的要求(图2)。
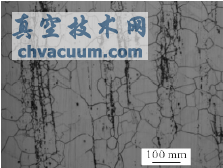
图2 主汽阀阀杆金相组织
通过扫描电镜背散射像进一步观察主汽阀阀杆的显微组织,发现其基体中分布有大量的黑色和白色的颗粒,尺寸在10μm量级,且形状不规则(图3(a))。EDS图谱表明这些颗粒是富Al、富Si、富Ti和富Mo的强化相,其中富Al颗粒尺寸较大,如图3(b)中“1”所示。富Si颗粒外形较细长,如图3(b)中“2”所示。富Ti颗粒外形接近圆形,且尺寸较小,如图3(c)中“3”所示。富Mo颗粒是白色的,外形多为圆形,如图3(c)中“4”所示。各强化相的合金成分见表2。
表2 高温阀杆各析出相成分 at%
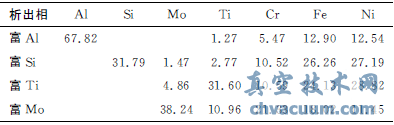
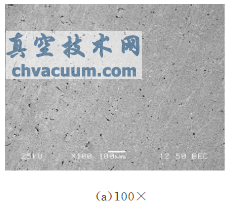
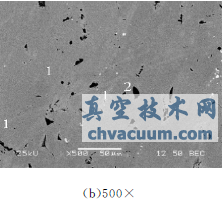
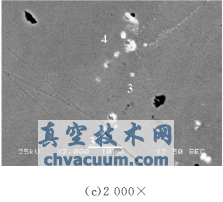
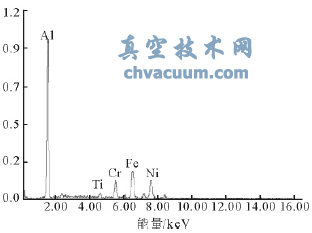
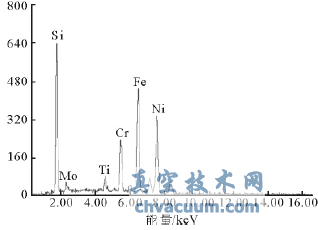
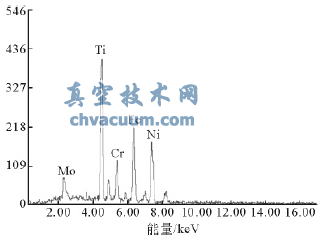
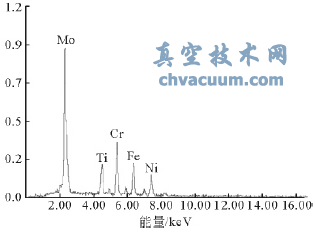
图3 主汽阀阀杆背散射相及标记为1~4的颗粒能谱
依据《手册》标准热处理状态下GH901组织为奥氏体基体上析出球状的γ'相以及少量的MC和M3B2等相。γ′相弥散分布于晶内,直径约为14~20mm,约占合金重量的10%~12%,其化学组成近似为(Ni0.95Fe0.03Cr0.02)3(Ti0.85Al0.15)。MC和M3B2相的总量约占合金重量的0.27%~0.35%。通过比较发现,GH901主汽阀阀杆中的各强化相颗粒与标准热处理状态下的强化相不符,说明断裂的高温阀杆热处理工艺不到位,微观组织异常。
5、力学性能
主汽阀阀杆横截面的布氏硬度值为360HB,满足《手册》对GH901合金硬度的要求(302~388HB)。
主汽阀阀杆的室温拉伸数据见表3。由表3可见,主汽阀阀杆的抗拉强度符合《手册》要求,但表征材料塑性的延伸率和断面收缩率均低于《手册》要求,这说明主汽阀阀杆母材的塑性较差。
表3 主汽阀阀杆室温拉伸力学性能
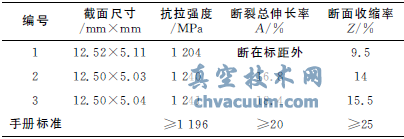
主汽阀阀杆试样的平均冲击功为41.5J,冲击韧性为518kJ/m2,低于《手册》要求的600~700kJ/m2,说明主汽阀阀杆母材的冲击韧性较差。
图4(a)是冲击试样断口的形貌,宏观断口比较平坦,呈铁灰色,无明显的纤维区和放射区。微观断口显示断面为典型冰糖结晶状,属于脆性沿晶断裂模式。断面上分布有不少的沿晶二次裂纹(图4(b~c))。同时,沿断口晶界上存在不少的颗粒和其剥离遗留下来的孔洞(图4(d))。
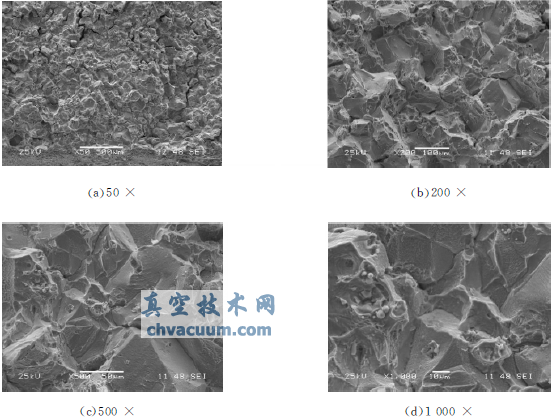
图4 冲击试样断口的二次电子相形貌
图5(a)是图4(d)的背散射图,通过EDS探测这些颗粒是富Mo、富Ti和富Al的强化相(图5(b~c)),这些强化相颗粒分布在断口的晶界位置,会进一步恶化基体的韧塑性。
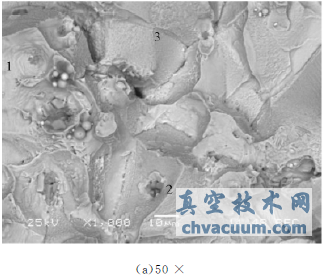
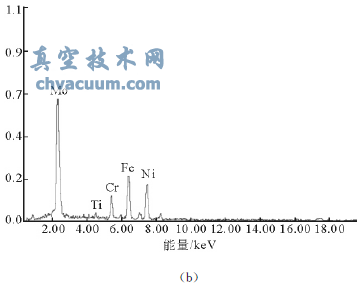
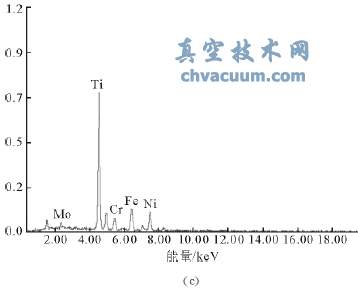
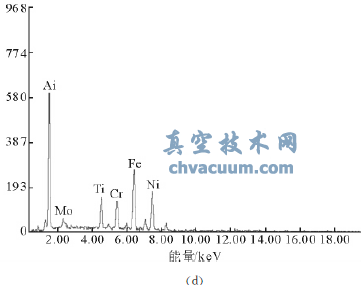
图5 冲击试样断口强化颗粒分布形貌及标记为“1~3”的颗粒能谱