浅谈电动执行器过力矩保护的发展
过力矩保护是电动执行器的一个重要控制环节,它的控制精度直接决定着执行器能否对自身和连接的阀门起到保护作用。本文从三种主流过力矩保护方式的优缺点及控制精度等方面进行对比和分析,以判断过力矩保护的发展方向。
电动执行器作为工业过程控制系统中一个十分重要的现场驱动装置,广泛应用于电力、冶金、石油、化工等行业。在流体控制中如阀门在运转中出现问题,就会在电动执行器中体现出来。所以它还拥有一个身份——“阀门的保护者”,其作用就体现在对阀门的正常使用的监测,其中很重要的一点就是过力矩保护。
顾名思义,过力矩保护就是指电动执行器在运行过程中一旦出现负载转矩超过允许的数值,应立即切断电源或者发出报警信号,进而停止电机的转动,以达到保护阀门同时保护执行器自身的目的。
作为现场仪表的一种,电动执行器的价值更多地体现在稳定性、可靠性和控制精度上。随着技术的发展,对执行器的要求早已超越了运转的稳定和可靠,对控制精度的要求越来越高,而过力矩保护在控制精度中占有极为重要的位置。在我国,电动执行器发展相对较晚,在过力矩保护方面就体现得更为明显。我们姑且把发展阶段按过力矩的发展状况分为三个阶段:机械控制过力矩阶段、传感器控制过力矩前期、传感器控制过力矩后期。在各项技术发展飞速的今天,我们的过力矩保护将走向何方呢?
1、机械控制过力矩阶段
我国从六十年代末七十年代初开始仿制前苏联的电动执行器,经过二十年缓慢发展,到八十年代生产出DKJ型角行程、DKZ型直行程电动执行器(我国唯一生产的电动执行器)。那个时候电动执行器在我国尚在推广之中,仅仅用来在特殊环境下代替人工作业,更谈不上过力矩保护功能,只能依靠设计时电机的功率来保证对力矩的控制。后来引进伯纳德电动执行器的技术,出现了最早的过力矩保护,其控制方式就是机械控制过力矩方式(后文介绍和分析的是在此基础上加以改进的控制过力矩方式)。这种方式的主要部件是力矩簧、传动件、行星内齿圈、力矩微动开关。见图1。
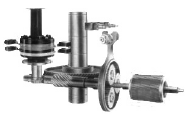
图1 电动执行器减速器部分结构简图
1.1、控制原理
电动执行器带负载运行,与电机连接的行星内齿圈随着转矩的传递,根据传递转矩的大小,轴侧力出现微小的偏转,偏转的幅度几乎与负载所产生的转矩大小成正比(具体计算在这里省略)。
所以一旦负载超过允许的最大值,拨动装在内齿轮外沿上的装有平衡正向和反向两个转矩的两个螺旋圆柱弹簧(简称力矩簧组件)的传动件,使力矩簧组件整体左右移动。当过力矩时,传动件带动连杆触动该方向上的力矩微动开关动作,产生瞬时电信号。在这里就有一个问题,如果电动执行器过力矩只报警一下,那就根本无法符合实际运转要求,故要借助控制电路板中专用的继电器来协助完成,从而使电动执行器停止运转。见图2。
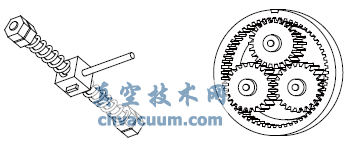
图2 力矩簧组件和行星盘组件示意图
1.2、控制精度
控制精度一般在10%到25%之间,而且随着负载的转矩的变小,变得越来越差。
这种过力矩保护方式是电动执行器发展到目前为止唯一的机械控制过力矩方式,与电气控制部分、电机、减速器部分有机结合和连接。
1.3、缺点
这种机械控制方式主要存在三方面的问题:
1)力矩簧的材质——弹簧的弹性系数在整个控制过力矩过程起着重要的作用;传动件的加工精度——传动件是保证连杆、力矩簧、传动件三部分保持相对受力平衡的关键部件。以上两点,任何一方面都足以影响整个过力矩控制过程。
2)机械部件在长期频繁使用状况下显得寿命相对较短,随着使用时间的加长,故障的出现率也会越来越高,同时大大影响过力矩保护控制的精度。
3)在现场安装执行器需要根据不同的要求的保护转矩值来对传动件的位置和力矩簧的松紧程度进行有效调节,而这样的机械控制方式需要打开控制箱部分的箱盖,最重要的是需要专业人员进行调节,非专业人员不易掌握,而且不易调节准确,造成较大误差。
之后也有一些制造商主动求变,将这样的过力矩保护方式结构做了一些改变,又将行星盘组件的位置做了一些改动,但实际效果大同小异,并没有实质的改变。目前的机械控制方式显然已经不满足现在的技术发展要求了,但作为唯一机械控制方式,仍可以控制过力矩的范围,而不作为精确控制。考虑到这种技术的成熟度和认知度,现在国内仍有广大执行器制造商使用此种控制方式。
2、传感器控制过力矩前期
随着电动执行器行业和现代工业控制计算机的发展,仪器仪表行业整体综合各项技术在不断上升,微电子技术和计算机等信息技术在仪器仪表行业逐步开始应用,出现了新式的智能型执行器,适应能力、自身应变能力相对原有的老品DKJ、DKZ更强,控制精度自然相应提高。单单依靠机械和电路板的组合才能完成的过力矩保护已经不能适应了,控制精度也不能完全达到要求,而一些制造商所做的一些改进也没有特别明显的提高,就迫切需要一种新的实现过力矩保护的方法,既可以独立完成过力矩保护功能,也可以配合控制板做到更好的控制精度。当时有一些厂家尝试将监测用传感器应用于电动执行器内部以提高测量精度,而过力矩保护是其中一个重要测试点,是一种新的尝试。此后不久,就出现了一种新的方式。
2.1、应变式模拟扭矩传感器测量原理
应变式扭矩传感器的测量原理是采用应变片电测技术,在弹性轴上组成应变桥,向其提供电源即可测量该时刻弹性轴受扭矩的电信号,进而得到扭矩值。见图3。
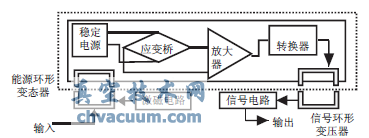
图3 应变式模拟传感器测量原理图
2.2、控制原理
由之前的传感器测量原理可以得知,该控制方式主要思想是将执行器上承载的负载转矩转变为电信号。它依靠接触式测量,也就是直接测量,主要有两种:第一种是将电动执行器的输出轴设定为弹性轴,将应变片组贴在输出轴上(见图4);而第二种是在遇到大的转矩才会使用带有转接轴套的扭矩传感器,通过传感器内部自带的弹性轴来完成转矩的测量。当执行器带负载运行时,应变片组将输出轴受到的转矩而造成的细微的形变转变为电信号,通过信号处理电路得到此刻的扭矩值。信号继续通过判断电路,一旦超过负载的最大值,独立的控制电路就自行切断电机电源,也可以通过输入保护信号到控制中枢电路,间接停止执行器的运转。
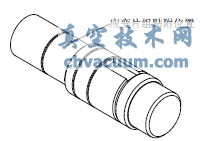
图4 应变片贴附位置示意图
2.3、控制精度
该过力矩保护方式相比以往的机械控制方式,控制精度有了明显的提高,可以达到10%左右,控制精度最高的可以达到7%。该过力矩保护方式不同于以往的传感器应用,将检测电子技术与过力矩控制尝试结合,既可以独立起到控制保护作用,也可以配合控制中枢电路板。这样的保护控制方式可靠性高,目的性更强,更有针对性。
2.4、缺点
这种电子式控制过力矩方式同样存在四方面的问题:
1)直接测量控制中,传感器中的应变片组要随着输出轴旋转,对于整体传感器的结构要求更高,对于安装环节也同样有着较高的要求。但是在旋转动力传递系统中,最棘手的问题是旋转的输出轴上的应变桥的桥压输入及检测到的应变信号输出如何可靠地在旋转部分与静止部分之间传递,通常的做法是用导电滑环来完成。由于导电滑环属于磨擦接触,因此不可避免地存在着磨损并发热,因而限制了旋转轴的转速及导电滑环的使用寿命。及由于接触不可靠引起信号波动。
2)而对于过载方面的调节,如果出现瞬间的高负载转矩,那么很有可能瞬间过载而损坏传感器,导致过力矩保护失效。在导致高负载转矩的各种原因中有一种是来源于自身的,就是死点。而在机械系统中死点广泛存在,且无法彻底消除,那么执行器配套的减速器部分的死点同样存在,所以对于死点位置的把握就成为这样的控制方式附加的一个问题。
3)应用电子控制,就不能回避干扰的影响。通过模拟测量原理图很容易看出,这些影响有可能来自外界,也有可能来自电路或者执行器内部。执行器可能存在于各种条件残酷的环境,比如高低温、高压、高空、密封等,如何处理干扰,把影响降低到最低,也是一个亟需解决的问题。
4)较高的制造成本也成为制约其发展与广泛应用的因素之一。
为了缓解干扰、提高控制过力矩控制精度,数字式扭矩传感器开始代替模拟式。对于传感器中的导电滑环,我们曾经专门做过实验,使用无线电遥测的方法,将扭矩应变信号在旋转轴上放大并进行V/F转换成频率信号,通过载波调制用无线电发射的方法从旋转轴上发射至轴外,再用无线电接收的方法,就可以得到旋转轴受扭的信号。尽管原理上可行,但遗憾的是这样的实验失败了,在执行器减速器箱体内狭小有限的空间内增加测量装置,而又不能影响其运转,显然难度太大了。
3、传感器控制过力矩后期
随着仪器仪表行业进入高速发展阶段,电子技术、信息处理技术、工业控制计算机技术趋于成熟,各方面技术的配合应用更加灵活,模块的出现就是一个标志,隔爆型、智能型等都陆续推出了改进型,综合能力更强。来自国外的先进技术使执行器行业进入了一个崭新的阶段,行业竞争压力陡然加大。智能通信、智能控制、总线、防护等级迅速提高,要求控制精度进一步提高。在过力矩保护方面,无法应对高过载和有效抵抗干扰已然成为制约控制过力矩精度进步的一道坎。国外的同行业厂家依靠先进的基础技术领先国内很多,这方面的技术更加成熟,所生产的产品更加稳定可靠,具有更好的性能与控制精度,更具有竞争力。
在这样的背景下,在起重机技术所应用的力矩限制器(TSFTST)的一些设计思路和技术应用到了电动执行器的过力矩保护中。
在这种思路的基础上,对于直接测量所出现的无法有效解决的各种问题,设计思路就转变为间接测量,出发点就是电机。近两年国内厂家出现了从电机入手的新式过力矩保护控制方式,也就是力矩检测电路。它的有些功能和结构类似TSFTST。在结构方面,有单片机、传感器等。在功能方面,当实际负载为额定负载的90%以下时,显示器“正常”灯亮;当实际负载达到额定负载的90%时,显示器“90%”灯亮,同时开始间断鸣叫预警;当实际载荷达到额定载荷的100%时,显示器“100%”灯亮,同时开始间断加快鸣叫报警;当实际载荷达到额定载荷的105%时,显示器“105%”灯亮,同时长鸣报警,继电器动作,电动执行器停止工作。目前的OSTO检测电路基本可以达到这样的功能。它们的主要部件有电压传感器、电流传感器。
3.1、控制原理
执行器运行中电机的电磁转矩与执行器的输出转矩是成正比的,执行器在运行过程中一直在克服负载转矩做功。
电机的电磁转矩公式为:TKI=Φcosθ。其中,K为比例常数,I为电机转子的电流,Φ为电机气隙旋转磁通的辐值,cosθ为电机的功率因数,θ为电机气隙磁通与转子电流的相位差。K比例常数可以通过在厂内实验得到。考虑到I电机转子电流不易测量,定子电流与其相差很小,故用测量定子电流来代替Φ磁通可以通过在定子绕组中增加简单绕组来得到。
cosθ电机功率因数需要利用单片机来计算,通过电机的三相电压和电流公式可以得到功率因数等于电机中任意一相的线电流与其他两相线电压的夹角的正弦值。利用单片机的计算能力和过零比较电路可以轻松计算得到。得到电机的电磁转矩,再经过计算电路得到输出转矩,从而判断此刻传递的负载转矩是否超过容许转矩的最大值。见图5。
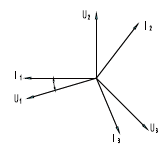
图5 电机相电压、相电流矢量示意图
3.2、控制精度
最大控制精度误差可以小于8%。运用单片机强大的运算能力配合电压传感器和电流传感器自身具有的抗干扰能力,对于整体测量的精确度起着很重要的作用,并且对于高负载的转矩的承受能力很大,不易损坏。
3.3、缺点
这种方式的缺点有:成本高,推广仍需时间;整体电路的运算负担很重,使用寿命受影响;同时使用两种传感器的话,尽管每种传感器的测量精度都很高,两种传感器的配合仍不可避免,又得经过D/A、A/D的转换,最后的控制精度仍然受影响。
面对这样的缺点,在今年初出现了简化电路的做法,主要出发点在于减轻电路的运算负担。如果能够通过I、Φ、θ中的一、两个变量来获得转矩T,则既可降低电路的硬件成本,又可减少微处理器的计算工作量。作为过载保护来讲,由此带来的测量精度下降,是完全可以接受的。依据这一思想,对执行器进行逐点测量获得了T与I、T与Φ和T与θ的若干条关系曲线(见图6),经过对比发现T与θ的关系具有较高的灵敏度,且在执行器输出额定转矩与空载转矩之间,θ的变化范围为:20°<θ<90°,可以作为测量T的依据。
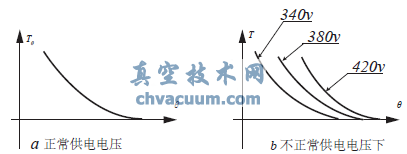
图6 T与θ的关系曲线示意图
通过纯数学——最小二乘法的方法解方程(具体计算这里省略),有效地消除不易测量的转子电流等未知量,可以降低成本,减轻电路的运算负担,同时增加整体过力矩保护电路对电压的适应能力。这种方案由于刚刚开发出来,尚在实验中,具体的使用效果暂时还不好下结论。目前有回归最早机械过力矩方式的办法,还有在原有基础上配合单片机的综合计算能力来提高控制精度的方法。总之一个宗旨就是提高控制精度。
4、结束语
从过力矩保护的发展脉络可以很清晰地发现,整体功能的强化、多样化、简单化、小型化贯穿始终,且还在持续。而近两年发展的一个主题就是智能化。在我们看来,真正的智能化主要还是在于应变,电动执行器面对不同的条件和环境,自身要具备应变能力。不管过力矩保护还是电机热保护、高温和低温保护,我们需要增加执行器的适应能力和自身保护能力。我们认为未来要以自身应变能力为主要开发点。单从过力矩保护来看,不管最早的机械式过力矩保护方式还是目前的利用传感器、单片机运算电路来完成力矩保护,都是不完整的。我们的思考方式要更加多元化,充分开发单片机的逻辑判断能力,利用执行器自身的判断能力。我们所需要做的或许是仅仅利用高精度转速传感器测量输出轴的转速,充分利用单片机的运算能力就可以完成过力矩保护的全部过程。至于效率、功率因数那些不可回避的问题,我们完全有能力绕开它们。不拘泥于一点,用发展的眼光看事物的发展,用全新的思维方式使繁琐的系统机构简易化,这是一种趋势。