电动执行机构多微处理器的控制方法
智能型电动执行机构功能齐全,给工业生产现场的运行和维护带来了极大的便利。然而,目前市场上的智能型电动执行机构还无法达到能同时满足适应大部分工况条件以及性价比高的要求,为解决智能型电动执行机构在工业生产现场的匹配,提出基于多微处理器模块化设计方法,通过不同模块的组合,可以实现不同要求的控制功能。将控制系统分三大模块及其控制软件,即人机对话模块、系统控制模块(主控制、电机驱动、故障诊断报警、信号反馈、系统通信等)、数据采集模块(阀位信号采集、力矩信号采集、远程开关量信号采集、模拟量信号采集)和系统控制软件。智能型控制系统通过模块间协同工作、合理调配,实现了阀门电动执行机构控制系统的智能化、通用性强、高可靠性和易维护的要求。
1、多微处理器模块化设计原理
智能型电动执行机构控制系统的人机对话模块、系统控制模块、数据采集模块各自具备一片微处理器,各处理器负责完成各模块的调度、控制功能,以系统控制模块为主机,其余模块为从机,通过UART口或I2C串行总线,根据通信协议,完成各模块间的数据通信与控制功能。系统设计原理框图如图1所示。
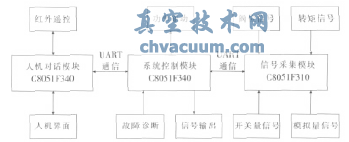
图1 控制系统原理
2、人机对话模块的设计
人机对话模块具备状态显示、参数组态、浏览、红外遥控等功能,硬件部分由显示屏、就地操作按键、指示灯、红外发射与接收设备等组成。采用C8051F340单片机实现人机对话功能。C8051F340的I/O口可以作为就地操作按键的输入口,也可以作为状态指示灯的输出口,完成显示屏的显示功能。模块通过UART口实现红外数据的发送与接收,图2为人机对话模块的红外发射电路。
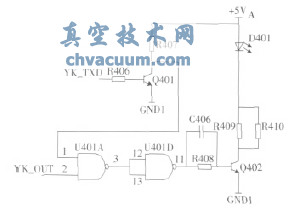
图2 红外发射电路
3、信号采集模块的设计
信号采集模块主要实现阀位信号和转矩信号的采集。智能型电动执行机构的阀位传感器主要分为两种:增量式传感器和绝对编码器。增量式传感器结构相对简单,信号稳定,数据处理比较容易,但在主电源断电情况下,需要电池供电保持阀位计数,一旦电池电压过低或无法供电,电动执行机构阀位容易丢失,给现场生产运行带来不便。绝对编码器由于每一个位置对应不同的编码,具有阀位记忆功能,所以无须电池供电,也不会出现阀位丢失现象,但绝对编码器对硬件和软件要求较高,特别是容易出现误码,需要进行软件处理才能使用。图3为增量式传感器的信号采集电路。
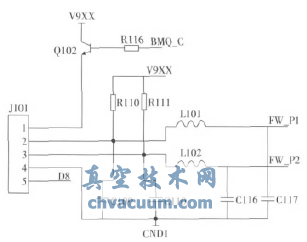
图3 阀位信号采集电路
在正常运行状态下,当BMQ_C引脚为低电平时,三极管Q102导通,V9XX为阀位传感器供电,当阀位发生变化时,阀位传感器输出两路正交脉冲,脉冲信号如图4所示。
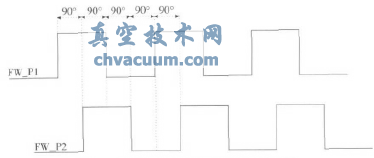
图4 阀位传感器脉冲信号图
信号采集模块中通过微处理器的I/O口采集阀位传感器的脉冲信号,通过数据分析,计算出当前阀位状态,然后通过串行总线,将阀位数据传送至系统控制模块,系统控制模块再将数据传递到人机对话模块,通过人机界面显示出当前阀位状态。
智能型电动执行机构的转矩可分为机械转矩和电子转矩,机械转矩简单可靠,依靠转矩开关的动作来判断转矩是否达到设定值,对机械零部件加工、装配的要求较高;电子转矩采用电子元器件的弹性形变产生的电压信号传递转矩值,使用前需要进行转矩标定,对信号采集模块的软件要求较高。在符合标准的转矩要求下,采用机械转矩即可满足智能型电动执行机构转矩控制要求。信号采集模块可将转矩动作信号传递至系统控制模块,从而控制电机的开、关、停操作。
智能型电动执行机构控制系统在远程状态时,通过开关量信号输入硬件电路,接收开、关、停指令信号,控制电动执行机构完成相关动作。为避免外部信号干扰,信号采集模块通过光耦N109、N110、N111将远方开关量输入信号进行信号隔离,隔离后的开关量信号接入单片机的IO口。IO口配置为弱上拉、开漏方式。在软件控制方式中采用“去抖”处理方式,能准确、及时采集开关量输入信号,有效避免误操作,提高电动执行机构运行的可靠性。为防止由于外部接线错误而导致硬件电路损坏,采用二极管VD111,有效避免接线错误带来的影响。
4、系统控制模块的设计
系统控制模块主要实现电机驱动功能和故障自诊断报警功能,并通过串行总线,读取信号采集模块的数据信息,处理后再发送至人机对话模块。
功率驱动信号控制电路实现硬件互锁功能,避免触发信号同时有效导致控制回路紊乱。利用C8051F340单片机三路IO口作为功率驱动电路触发信号,一路IO口作为触发信号输出端电源控制信号,另两路作为触发控制信号,进一步提高触发信号可靠性。IO口配置为推挽方式,低电平有效。采用光耦TLP521-4对触发信号进行信号隔离,避免触发信号干扰,保证电动执行机构可靠、稳定运行。
系统控制模块还具备故障自诊断与报警功能,在判断出故障现象时,根据故障优先级及安全保证,可采取不同控制方法,选择保位或运行至指定位置,同时,输出故障状态信号,并在人机对话界面显示故障代码。