低压降水封阀的开发和应用
针对现有催化裂化装置能量回收系统水封罐压降大的缺点,开发设计出一种新型低压降水封阀。文中描述了新型低压降水封阀的原理和新、旧结构压降数值模拟分析结果及其工业化应用。该新型水封阀的应用实践证明,该设备具有安全、可靠、低压降和节能的优点,具有较高的工业化应用价值。
催化裂化装置中,以烟气轮机作为主要设备的能量回收系统,在提高企业经济效益方面占有重要位置。催化装置中的水封罐虽然是整个烟气能量回收系统的辅助设备,但却是保证该系统安全、长周期运行的主要条件之一。原有传统结构的水封罐(传统水封罐结构见图1)虽然具有安全性高、操作方便、结构简单等优点,但同时也具有压降较大,致使烟气轮机出口压力较高,进而影响了烟机最大限度的回收能量。
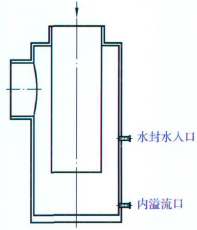
图1 传统水封罐外形示意
烟机功率公式为:
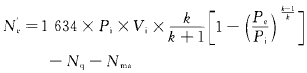
式中:Nc——烟机实际轴功率,W;
Nq——烟机壳体经辐射和对流传出热量的当量功率,W;
Nma——轴承消耗功率,W;
Pi——烟气人口压力,Pa(绝);
Pe——烟气出口压力,Pa(绝);
k——烟气绝热指数;
Vi——烟气人口状态流量,m3/min。
由此可见,如果降低烟气轮机出口压力,即烟气轮机后续设备、管道等压降减小,即可提高烟气轮机功率。因此开发一种新型低压降水封阀,具有非常现实积极的意义。故某公司在保证催化裂化装置水封安全可靠的基础上,开发出新型低压降水封阀。
1、新型低压降水封阀的开发
1.1、传统水封罐压力损失分析
传统水封罐在正常工作时,烟气经过烟道从上方进人水封罐内筒,经内筒折返后流经内外筒夹套后流出。由于水封罐烟气进!出口管道必须90°或180°布置,烟气正常输送时经历了扩口减速、扩容、180°转向、缩口加速等过程,造成烟气正常通过水封罐时压力损失。正常情况下压力损失在2~4kpa。
1.2、新型低压降水封阀工作原理
新型水封阀的设计必须依据如下原则:
(1)安全可靠,密封严密;
(2)压降低,即压力能损失小。
在此原则指导下,设计了一系列结构方案,并作了详细的理论分析和计算,最后采用了内筒浮动式密封结构,如图2所示。
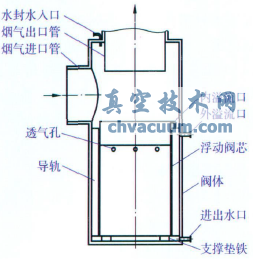
图2 新型低压降水封阀无水封时示意
该水封阀主要利用了流体浮力驱动和水封原理,利用浮力将阀体内的浮动阀芯浮起,浮动阀芯上部有水槽,浮起至烟气出口管下端时,阀体上部有水封水人口对浮动阀芯上部水槽注水,水槽与烟气出口管联通,烟气出口管中液位在烟气进口管压力的作用下上升,升至与烟气进口管压力平衡的液面,达到切断烟气的目的。
如需开启气相介质通道时,将水封水入口关闭,排水口打开,阀体内水外排,浮动阀芯沿导轨下降,落到阀底部的支撑垫铁上,此时气体进口管和气体出口管直接联通,整个管路开启(见图3)。
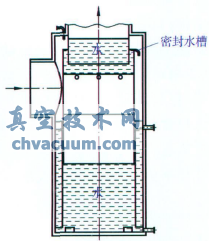
图3 新型低压降水封阀开启水封时示意
2、传统水封罐和新型低压降水封阀压降的数值模拟分析
为了比较传统水封罐和新型低压降水封阀的压降,验证新型低压降水封阀结构的合理性,以山东某炼油厂1400kt/aDCC装置为例,对这两种结构作了数值模拟:(1)两个对象的网格划分方式相同!网格密度一致,采用湍流模型、离散格式;(2)计算条件为:固定进口压力8.9kPa(表压),温度943K;烟气流量:2854m3/min(标准状态);出口温度:803K,烟气按空气考虑。
根据计算结果(见图4与图5),在完全相同的计算条件及网格密度下,旧式水封罐的总压损失为19OOPa,而新式的总压损失仅370Pa。从新旧结构速度分布矢量图上可以看出,旧式结构中存在流体在底部急剧减速后进人内外筒环隙急剧加速的过程,此部分压降损失占总压损失较大比例,而新式结构无此部分损失,另外新式结构流体流路较短且顺畅,漩涡和滞留区较少,通过数值模拟分析,可以肯定新型低压降水封阀压降是比较低的。
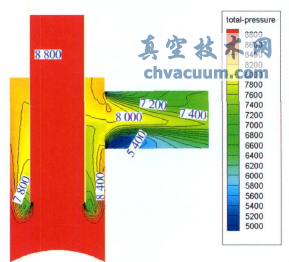
图4 传统水封罐某个截面上的总压损失分布
(进出口面平均总压差即总压损失为1900Pa)
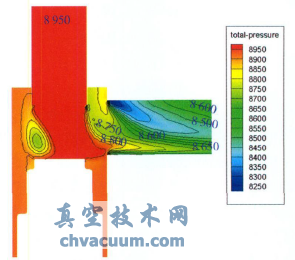
图5 低压降水封阀某个截面上的总压损失分布
(进出口面平均总压差即总压损失为370Pa)
3、安全可靠性分析
为了论证新开发产品的安全可靠性,进行了设备故障可能性分析和工艺事故状态设备可靠性分析。
3.1、设备故障状态分析
根据该水封阀结构的特点,比较容易出现的问题是内浮筒热变形!受压失稳!导轨受热弯曲变形等,这些问题会导致浮筒卡死或无法对应进人上部烟气人口管,无法达到建立水封截断烟气的目的。针对此问题,设计时主要采取以下措施来保证设备平稳运行:
(1)浮筒设计时进行详细的应力分析,保证浮筒有足够的刚度和强度以抵抗失稳变形和强度失效;浮筒设计时考虑热应力及局部热膨胀变形,浮筒底部、变径段及密封水槽等部位全采用柔性结构,以降低热应力及局部热变形,并在制造过程中进行泄漏试验。
(2)严格控制导轨变形,并将其控制在一定范围内,特别不能限制其长度方向膨胀,否则导轨会弯曲,影响浮筒上浮。所以导轨设计为分段重叠型式,分段导轨两端自由膨胀,中间支撑采用非焊接结构固定。导轨导向的精确性主要通过控制导轨与浮筒的间隙来确保,其间隙约为浮筒膨胀量+浮筒不圆度公差+经验裕量,保证浮筒上浮过程中最大倾角小于1(°)。
(3)在水封阀内部设置内浮筒高度位置锁紧机构,水封阀水封效果建立后,可启动锁紧机构使内浮筒固定在相应位置,以防止意外情况下内浮筒跌落,水封被破坏,泄漏烟气造成事故。
3.2、工艺事故状态下设备可靠性分析
正常工况下烟气轮机出口催化剂粉尘浓度小于200mg/m3(标准状态),并且10μm以上的颗粒小于3%,另外低压降水封罐烟气进出口压降低,烟气流通比较流畅,滞留区少,携带能力大(烟气流速在30m/S左右),故积灰的可能性较小。但如果装置操作不正常,大量催化剂会进人水封阀,如果不清理,会在浮筒上结垢,堵塞浮筒与导轨间隙,导致内浮筒难以浮起,所以水封阀下部设置催化剂清除口,可用高压水清洗后放出,从而提高可靠性。
另外,从中石化镇海炼化分公司使用一年后停工检查、试验结果看,内浮筒和导轨无明显变形、扭曲,冲水试验水封阀工作正常,实际应用效果证明,该新型水封罐具有较高的可靠性。
4、工业化应用
中石化镇海炼化分公司2007年11月5日烟机后路压力突然下降5kPa,检查后发现为原传统水封罐内筒脱落所致。内筒脱落后烟气不再经内外筒间的环隙折流,而是直接侧向进人,向上出水封罐,与新型低压降水封阀烟气流路相同。2009年5月中旬在3000kt/a催化裂化装置长周期运行及节能改造项目中,将余锅进口水封罐改造为新型低压降水封阀,改造后烟机后路压力与2007年n月5日后相同"该结果说明,新型低压降水封阀与传统水封罐相比压降减小约5kPa,经过三个多月的运行观察,烟气轮机输出功率明显提高,电动机耗功显著降低,从而整个装置的耗能减少"改造前后的运行工艺操作参数对比见表1。
表1 改造前后烟气轮机工艺操作参数对比
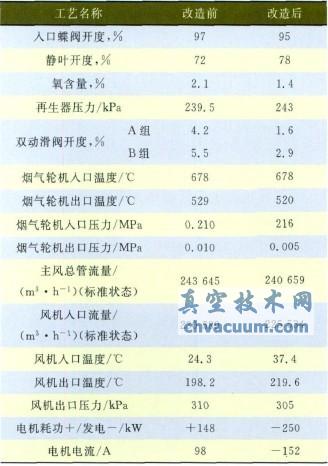
从表1可以看出,改造前后在主风流量、主风机出口压力、再生器压力、烟气轮机入口压力、烟机入口开度等变化很小的情况下,烟机出口压力出现明显的降低。从电机耗功和电机电流数据可以看出,改造后烟机做功增加,除满足电动机需求外多发电250kw。从而减少整个装置的能耗,创造经济效益每年约514.4万元,经济效益显著。
5、结语
在催化裂化装置能量回收系统中,应用新型低压降水封阀,压降比传统水封罐将低80%以上,假定3000kt/a催化裂化装置有4000m3/min(标准状态)烟气量,依据以往操作取得的经验,背压每降低1kPa,电功功耗下降120kw左右。因此通过应用新型低压降水封阀来降低烟机背压对降低装置能耗效果显著;同时,降低能量回收系统的背压,对催化裂化装置未来配备烟气脱硫等其他装置提供了压力和动能,为避免更换主风机等设备提供了可能性。然而该水封阀也具有造价较高!结构复杂等缺陷。综上所述,该新型低压降水封阀具有广阔的工业化应用前景。
参考文献:
[1]习杨青,祁鲁海.催化裂化烟气轮机人口管道的设计[J].化工设计,2004,14(3):28一31.
[2]曹汉昌,郝希仁,张韩.催化裂化工艺计算与技术分析1M2,北京:石油工业出版社,2000:490一495.