基于UG与Moldflow的汽车门槛饰条工艺优化及模具设计
以汽车门槛饰条为研究对象,分析其结构和成型工艺,确定注塑模结构为一模两腔。利用Moldflow 模拟分析,确定了浇口的最佳位置,分析了充填时间、熔接线、气穴等。结合模流分析结果,利用UG 设计了分别装在动模和定模的多个镶块的弯楔抽芯机构,斜顶侧向抽芯机构、自动顶出机构等。结果表明:该方案结构合理、工作过程可靠、能有效地缩短塑件的生产周期。
随着汽车行业的发展,人们生活水平日益提高,汽车逐渐成为了人们生活的一部分,人们对汽车的要求也越来越高,不仅要求汽车具有良好的使用性能,而且追求汽车具有良好的外形轮廓和舒适美观的内饰。文章以某型汽车门槛饰条为研究对象,采用计算机辅助设计软件UG 和有限元分析软件Moldflow相结合的方法对其进行注塑模具设计,旨在达到减少试模、改模的次数,缩短产品的开发周期,节省成本的目的。
1、塑件结构与工艺分析
塑件三维结构如图1 所示,塑件尺寸为1 773. 6 mm ×164. 9 mm × 109 mm,主壁厚3. 2 mm,最小壁厚1. 4 mm,材料为PP + EPDM + MD30。聚丙烯(PP)的主要特点是密度小,其力学性能如屈服强度、拉伸强度、硬度等均优于低压聚乙烯;并有突出的刚性,耐热性较好。通过对PP 进行弹性体改性(EPDM)和矿物质改性(MD30),可以在不明显降低其它性能的情况下,大幅度提高聚丙烯的抗冲击性能。
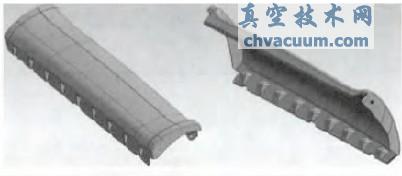
图1 塑件三维模型
门槛饰条由曲面构成,有形状不规则的孔及突起,左右不对称。根据成型塑件一侧壁上的方形通孔及两端通孔的需要,需要侧抽机构,另一侧壁存在倒扣,要保证塑件出模,需要斜顶机构。为了提高生产效率及使模具进料受力平衡,保证模具的强度,采用一模两腔,热流道转冷流道成型。
2、基于Moldflow 的模流分析
2.1、模型前处理
采用Moldflow CAD Doctor 导入塑件三维模型,去除对分析结果没有影响的小圆角、倒角、台阶等结构,并将修复完成后的塑件导入Moldflow 2012 中,提高网格划分的质量和效率。采用双层面网格划分,网格边长取8mm。划分网格后,模型网格匹配百分比和相互百分比达到92. 4% 和90. 5%。最后再修复自由边、相交单元、纵横比等缺陷,完成对塑件的网格划分。
2.2、确定最佳浇口位置
根据塑件结构和实际经验,预设了2 种不同的浇口位置方案,如图2 所示。方案一采用三点进胶,可以减短流程,易于模具设计;方案二则采用六点进胶,相近的两个浇口为一组,其作用相当于一个大的浇口,可以降低注射压力,且相邻两浇口距离近,熔料温度较高,浇口之间不会产生熔接痕。
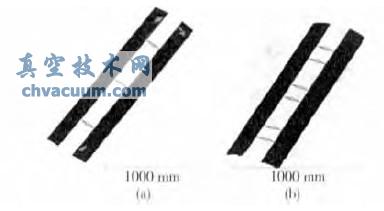
(a) 方案一;(b) 方案二。
图2 浇口布置方案
通过对两种方案添加浇注系统和冷却系统的填充分析,得到如表1 所示的结果。可以看出,无论是充填时间、注射压力、锁模力和达到顶出温度时间等,方案二的结果都优于方案一,因此选择方案二的浇口布置方式进行下一步的深入模拟分析。
表1 方案参数比较
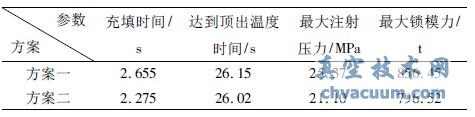
4、结论
文章综合使用了UG 和Moldflow 软件,针对汽车门槛饰条进行了详细的成型工艺分析、模流分析和模具结构设计,找出了在注射过程中的熔接痕、气穴等缺陷产生的原因,有效地保证模具设计的质量和效率,指导了实际模具设计和生产。