大口径液氢真空截止阀的结构设计
液氢截止阀按绝热形式分主要有外堆积绝热和真空多层绝热,本文主要针对该液氢阀门结构进行了分析。阀门在整体上采用了真空夹层结构,阀杆选用了波纹管密封结构,阀座和阀体一体加工成形,并且阀盖组件可以从阀体中整体抽出,方便的实现了阀瓣的快速更换和维修。该阀门结构形式已经申请国家专利(申请号:200720186326.3)。
在航天试验系统的各管路中,安装有大量的低温截止阀,结构形式主要以角式和直通式为主,口径≤DN200,压力≤PN25。而随着国家对新型氢氧火箭发动机研制的不断深入,对于氢氧用低温阀门也提出来了更多的要求。春中DN250液氢截止阀即是为了满足该需要,并应用于航天新一代YF-XX发动机全系统长程试验台液氢主管路加注用阀门。该阀门工作条件:口径250mm、压力1.0MPa、温度-253℃,阀门常开但要求紧急关闭后漏率符合GB4981A级要求,阀门流体阻力系数小。目前该阀门已经成功研制并应用于试验系统中。
1、方案确定
该阀门属于低温大口径阀门,对于低温阀门来说,漏热是问题的关键,尤其在液氢温度下,漏热问题更是突出,为了保冷低温阀门采取的绝热形式有堆积绝热、高真空绝热、真空粉末绝热和真空多层绝热。对比以上各绝热形式,对于液氢来说,阀门从整体结构上采用真空多层绝热比较经济,故阀门采用了真空多层绝热。
根据试验系统要求输送流体的阀门阻力系数要小,流体的波动要小,基于此,该阀门最好选用球阀和直流式截止阀。由于球阀一般为等径、同轴输送,流阻小,波动也小,所以在生产中得到了广泛应用。但是应用于低温的球阀往往由于材料的收缩使得阀门在低温下的泄漏不容易得到控制。所以阀门采用了直流式截止阀。阀门具体结构见图1。
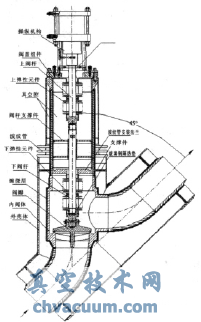
图1 阀门结构图
2、材料选择
因为低温阀不仅要求在低温下保证正常工作,同时也要保证其常温的工作性能,所以对于其所使用的材料不仅要满足常温机械性能,同时也要满足低温下所需的机械性能,尤其是冲击功(AKV)和相对延伸率δ5的要求。针对以上要求,对于使用在低温状态下的材料,为了防止材料在低温下的低应力脆断,我们一般多采用奥氏体组织的材料如:奥氏体不锈钢、铜及铜合金、铝及铝合金等。这是因为经过对低应力脆性断裂特点的研究,对金属断裂机理进行分析,发现金属的低温韧性,即缺口尖端处的金属微观塑性变形能力,是决定设备抵抗应力脆断破坏的能力。实验表明,具有面心立方结构的金属如铜、铝、镍和奥氏体类钢则基本上没有这种温度效应,即没有低应力脆断。这是因为当温度降低时,面心立方金属的屈服强度没有显著变化,而且不易产生形变孪晶,位错容易运动,局部应力易于松弛,裂纹不易传播,一般没有脆性转变温度。而不锈钢在满足相同机械性能的条件下,与其它材料相比具有价格优势,所以该阀门的主体材料选择了奥氏体不锈钢。
3、阀门结构
3.1、整体结构
由图1知阀门从整体上采用了真空多层结构,内、外阀体之间通过阀盖焊接连接,内、外阀体之间由温度梯度引起的变形通过波纹管补偿吸收。内外阀体之间的A腔抽空至1×10-3Pa,内阀体外璧缠绕多层绝热材料,外阀体内壁抛光。阀门出入口与管道采用焊接直接相连,并将保持A腔真空度的分子筛安装在管道上。阀杆轴线与输送方向成45°夹角,出口与进口采用弯头圆滑过渡以减少流动阻力。为了方便阀门维修,阀盖与阀杆在结构设计上采用了整体分离的结构形式,即阀盖和阀杆可以从阀体中整体抽出,其中阀杆的定位通过其整体结构上的套筒与阀体内壁的配合来实现。这样即便于阀杆的拆卸、密封面的维修更换又使得阀体的密封面和配合面的维修变得容易。阀门的操纵机构通过螺栓安装在阀盖上,并设计了安装在气缸支架立柱上的阀杆防转机构,防止阀杆发生周向转动破坏波纹管密封元件。
3.2、阀杆结构
阀杆采用了上下分段结构,上、下阀杆之间安装玻璃钢隔热垫来降低阀杆的漏热,两阀杆通过螺纹连接,两阀杆的对中由上、下阀
杆之间的光滑段保证。为了防止上、下阀杆之间的相互转动,在两杆之间套和的位置安装防转螺钉(具体结构见图2)。阀杆的密封采用了如图1所示的双波纹管结构,上、下波纹管为弹性元件,该弹性元件与波纹管的主要区别在于弹性元件可以实现波纹管的比例收缩,即受力与变形成正比关系。其中下弹性元件下部与下阀杆焊接,上部与波纹管连接件焊接连接,以此防止管道介质的外泄。上弹性元件下端与上阀杆下端焊接,上弹性元件上端与波纹管安装法兰焊接连接。该结构能够防止外界含水空气进入下弹性元件内部,引起下弹性元件内部结霜或爆炸而影响其正常工作。由于波纹管承受扭转的承载能力低,所以在安装两个波纹管弹性元件时要求其不承受附加外力的作用,设计防止阀杆转动的结构(见图1)。由于阀门口径较大,所需导热长度长,为此采用长阀颈结构而增加了阀杆长度,所以为了保证阀杆运动平稳并在不加大阀杆直径的前提下提高阀杆的承载能力又在阀杆中间位置设计了阀杆支撑件。由于不锈钢材料之间配对使用时容易出现咬合的现象,为了防止阀杆与阀杆支撑件的咬合,在支撑件上安装了黄铜,从而改善这种状况。黄铜摩擦套安装在支撑件的轴套上,其中轴套与黄铜摩擦套过盈配合,并在两件之间安装了防转螺钉,而阀杆与摩擦套之间采用间隙配合(具体结构见图2)。
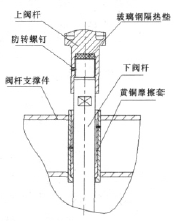
图2 阀杆支撑图
3.3、出入口结构及连接形式
传统直流式阀门其介质出入口与管道相连没有采用弯头圆滑过渡,使得输送介质的流体阻力、冲击比较大。为了改善该情况,设计完成了如图1所示的出入口采用弯头圆滑过渡的结构形式,该形式即降低了流体流动阻力,又能降低液氢在流动过程的波动。并且采用该种结构形式的阀门,其阻力系数ζ不会超过7。
在真空管道中,阀门与外部管道的连接方式不外乎两种:法兰连接和焊接连接。相对于液氢管道来说,为了降低漏热主要选用了真空法兰的连接方式,该种方式的优点就在于其阀门更换方便,拆卸阀门不破坏管道的真空。但是低温状态时,真空法兰的漏热会对于运行中管道系统的安全性造成很大威胁。而采用直接焊接连接结构,由于不存在液氢的外泄则不存在这种潜在危险。而为了实现阀门维修时不破坏管道真空的要求,在对阀门进行结构设计时设计了阀盖组件直接从阀体中整体抽出来的结构形式,而阀门的外壳及内阀体与管道连为一体。该结构为阀门的维修提供了更大方便。而阀门真空腔与管道真空腔形成一体的结构,更有利于阀门真空腔真空度的维持,并提高了阀门的真空使用寿命。
3.4、支撑形式
由于内阀体处于液氢温度范围,漏热问题就比较突出,而且在采用真空多层绝热结构中,构件的漏热占总体漏热的比重与高真空绝热或堆积绝热结构相比较高,所以为了降低漏热,内、外阀体的的支撑材料选用了导热系数较低(导热系数仅为0.25~0.45W/m•K)而强度相对较高的环氧玻璃钢,支撑件的具体位置见图1。
4、阀座结构和密封
对于阀座密封面的密封性能来说,阀座的变形将直接影响密封面的性能,所以阀座的结构设计应考虑其对刚度的要求,在满足强度的前提下更应考虑刚度的要求。而且阀座的制作加工过程即阀门配合面的加工质量对于阀门的密封影响也很大,尤其是阀杆轴线与阀座密封面的垂直度。所以阀座、弯头、内阀体焊接后整体加工,这样可以保证密封面与阀体轴线的垂直度和阀杆支撑件与阀体的同轴度,并通过定位筒与阀体、阀杆支撑件与阀杆的配合实现阀杆对密封面的垂直度要求以保证密封。在该阀门中涉及到的密封主要包括密封面密封、阀杆密封、法兰密封面密封三种。密封面的密封形式选用了广泛使用的平面软密封,而没有选择对中性较好的锥形或者球面密封,主要考虑到在低温状态下出现过阀瓣卡死在锥形座内的情况。而为了提高阀瓣的对中性能,在阀座上设计安装了阀瓣导向套(其导向长度不低于0.8D,且还应保证流道面积在减去导向套筋板所占面积后的实际流通面积不低于DN250的口径),并且阀体与阀座一体焊接后整体加工,以进一步确保密封面的密封性。阀杆密封则采用了以上已经谈到的上、下波纹管的密封形式,使介质实现了零泄漏。而法兰密封面的密封考虑到阀门处于低温状态,选用了比较常用的铝垫片平面密封。
5、结束语
采用上述结构的截止阀,已经完成多次发动机试验任务,阀门动作灵活、密封性能好、绝热效果明显,没有出现大面积的结霜现象,阀盖能够方便的从阀体中抽出进行维修。该阀门的成功研制填补了我国超低温大口径截止阀的空白,技术水平处于国内同行业的领先水平。