核级蝶阀阀体铸造工艺数值模拟
蝶阀阀体是蝶阀上的核心零部件,服役时承受高温高压,因而要求其组织致密,不允许有缩孔、缩松和气孔等缺陷。本文先用SolidWorks软件对蝶阀体进行实体造型,然后利用JSCAST软件对铸件进行充型和凝固过程模拟,预测铸件充型过程中可能产生的充填不良、裹气现象及凝固过程中可能发生缩孔、缩松缺陷的位置,然后对模拟结果进行工艺优化。模拟结果表明,改进后的铸造工艺能够实现平稳的充型,充型结束后铸件各部位温差较小;铸件能够顺序凝固,有害热节全部消失,缩孔或缩松缺陷也相应的消除。实际生产对模拟结果进行了有效的验证。
口径为1200mm的核3级蝶阀是阀门中有代表性的阀门,由于蝶阀铸件尺寸较大,形状复杂,截面厚薄悬殊。这类铸件常处于高温、高压工作状态,对其强度、刚度尤其是密封性要求非常严格。因此在铸造生产中严禁有缩孔、缩松和气孔等缺陷的产生。将计算机模拟与仿真技术应用于铸造业中,具有传统的“试错法”所无法比拟的优势。利用该技术,铸件的缺陷可以在生产前被有效预测,根据模拟结果,技术人员可以及时进行工艺改进,从而最大程度地避免铸件充型凝固过程中出现的裹气、充填不良、缩孔(松)、气孔等缺陷。在过去的几十年里,许多学者对这方面的工作进行了深入且系统的研究。但长期以来,铸造过程的数值模拟主要集中在凝固过程的模拟研究上,这就使得数值模拟只能对缩孔、缩松等缺陷进行预测,而对充型过程中产生的缺陷,如由于温度分布不均引起的气孔缺陷研究很少。本文利用数值模拟与仿真软件JSCAST对铸钢阀体的充型和凝固过程的温度场和流场进行了数值模拟,并根据模拟结果对原有工艺进行了改进,从而解决了铸件缩孔、气孔的问题。
1、蝶阀阀体模拟前处理
1.1、铸件实体造型
本文使用3D软件SolidWorks对零件进行实体造型,然后以STL格式导入JSCAST中进行铸型的定义及网格的剖分,为保证模拟的精度和计算的速度,选用等间隔的剖分方法将整体模型(铸件和铸型)剖分为细网格,再用增加/删除的网格修改方法将铸型部分的网格适当的放宽。根据铸件铸造工艺的特点,采用图1所示的铸造工艺设计方案。
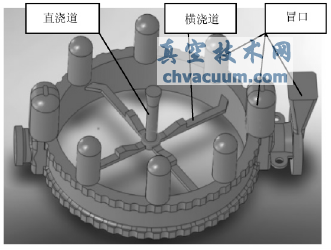
图1 阀体原始铸造工艺图
1.2、铸件边界条件的设定
铸件材料为00Cr25Ni7Mo4N制定出00Cr25Ni7Mo4N超级双相不锈钢的热物性参数如表1所示。
表1 00Cr25Ni7Mo4N的物理性能参数
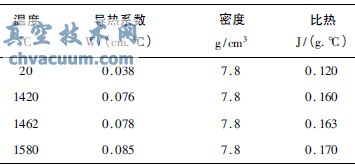
根据实际生产经验采用铸型材料为碱性酚醛树脂砂,该砂型在软件材料库中并没有列出,所以查阅相关铸造砂型的热物性参数后,得出了如表2所示的热物性参数,并将手动输入模拟软件中。设置材料的边界条件如下:铸件的浇注温度1580℃,铸型和冷铁的初始温度为20℃,铸件和冷铁之间的界面换热系数为1500W/(m2•K),冷铁及铸件和铸型之间的界面换热系数为1000W/(m2•K),直浇道顶面和空气之间的换热系数为650W/(m2•K),浇注速度为68cm/s,重力加速度为9.8m/s2。
表2 碱性酚醛树脂砂的热物性参数
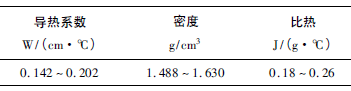
2、原始方案模拟分析
2.1、充型过程
铸件钢液沿着四个横浇道弯折30°,快速平稳地填充到型腔里,整个填充过程没有出现严重的飞溅和明显的浇不足现象。充型过程中,铸件温度场模拟如图2所示。
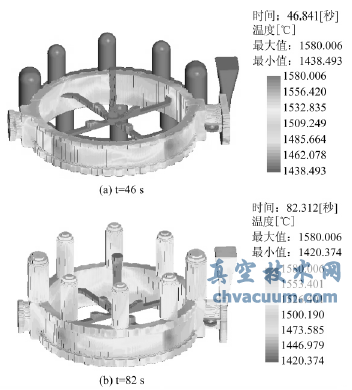
图2 充型过程温度场模拟
从图2(a)中可以看出,在填充时间为46s时,金属液已经充满整个型腔。此时铸件两端法兰处温度开始下降,约为1460℃,但铸件中部区域仍为纯液态,温度大约保持在1560℃。因此在铸件的中部区域和两端存在一个明显的温差,使得整个温度场传热不均匀,可能会在整个金属液态流变场中产生不均匀的流变应力,与液态金属中存在的空隙相互作用,形成各种气孔缺陷从而影响铸件的质量.因此需要在铸件的中部适当增加一些排气孔来消除气孔缺陷。
随着填充的持续进行,时间到82s时,铸件各部分的温度变化更加明显,如图2(b)所示。此时,大法兰处的凸耳已经凝固,两端法兰处出现固液两相共存区,即铸件已开始凝固。在此区域往往易发生非顺序凝固,有可能在成型铸件中出现浇不足,因此在此区域内要合理设计冒口以消除此类浇不足现象。
2.2、凝固过程
铸件凝固过程中固相率随时间变化的情况如图3所示。
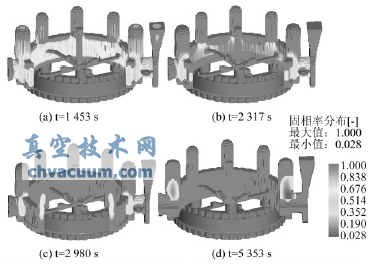
图3 凝固过程固相率分布情况
铸件凝固至1453s时,这一阶段主要是浇注系统、两端法兰薄壁处和型腔上下边缘先凝固。这些部位壁比较薄表面积比较大。从图3(b)可看出,型腔表面基本已凝固,内部还没有完全凝固,但并没有达到所要求的冒口之间的型壁先凝固冒口下方的型壁后凝固这一顺序凝固的要求。从图3(c)可以看出,铸件除了冒口内部没有凝固外其他部位都已凝固;圆柱形冒口与型腔相接触的部位形成了补缩通道,而未接触的部位已经完全冷却,这样冒口并没有对铸件完全补缩。从图3(d)可以看出铸件凝固至5353s时,只剩下椭圆形冒口根部没有凝固,而这一部位会形成大的热节,如果金属液中侵入气体很可能会在这一部位形成缩孔。
图4为凝固率与时间所对应的关系图。当凝固率约为95%时,凝固已接近尾声。在3190s有一个转折,主要是因为薄壁型腔先凝固与冒口之间未形成良好的过渡。可能因为补缩通道被堵,压力过小形成断流,或冒口位置不合理,或冒口尺寸太小而造成的补缩不足形成的。这样型腔部位极易产生缩松缩孔缺陷,需要通过设计冒口,控制铸件凝固速度来消除这些缺陷,以获得优质产品。
3、缺陷分析及工艺改进
3.1、缺陷分析
在冷却凝固成型过程中,当缩孔里边的空隙为金属液本身吸附的空气或二氧化碳所填满时,这样的缺陷为气孔。铸件在凝固过程中,由于发生非顺序定向凝固,也会产生热节缺陷。图5为铸件凝固过程中热节分布情况,图中浅蓝色显示铸件凝固至2317s左右时形成的热节,这些热节的形成主要是冒口补缩距离太短;冒口补缩距离短的原因是冒口与型腔没有形成有利的补缩通道以及铸件没有形成顺序凝固;所以需要改进冒口并添加补贴来增大冒口补缩范围和形成有利的补缩通道。由于型腔上下冷却较快,形成向中间缩小的温度梯度,中间部位又没有得到补缩,以至于形成大片的热节,这些部位形成缩孔的可能性很大。椭圆形冒口根部凝固至最后形成大的热节,这些热节温度较高,最后凝固,形成缩孔的可能性极大。
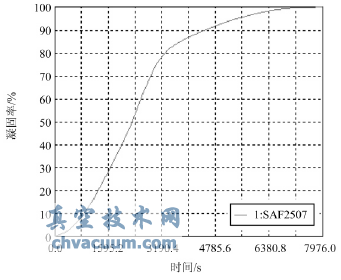
图4 固相率随时间变化图
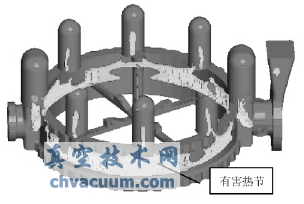
图5 原始工艺铸件热节分布图
3.2、工艺优化
针对原始方案中冒口补缩范围小、补缩距离短的问题,优化方案一中加大了冒口尺寸。在六个圆柱形保温暗冒口下面增加了补贴,来提高补缩效果,同时为了使浇注时间同原来保持同步,也加大了横浇道的尺寸。

图6 优化方案一铸造工艺图
从图7充型结束时温度场可以看出铸件的温度分布比较均匀,与原始方案相比有了很大的改善。主要是因为加大了冒口的尺寸后蓄热能力有了增强,同时加了补贴后冒口根部的型腔的温度和冒口保持一致,这样就会冒口之间的型腔会先凝固而冒口处后凝固从而形成顺序凝固,冒口的补缩效果更明显。
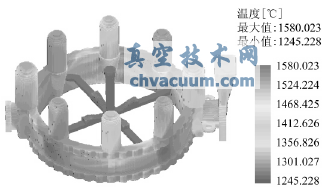
图7 充型结束时温度场分布图
图8为优化方案一铸件热节分布的结果,图中可以看出,冒口处均有热节而且是在时间较晚时形成的热节,主要是因为冒口芯部凝固的较晚,但这并不影响铸件的质量。但在冒口之间我们看到浅蓝色的区域为在时间比较早时产生的热节,这些热节的产生如果遇到侵入性气体也可能形成缩孔,所以必须将这些热节给予消除。我们看到这些热节上下均有分布,因此需要在这些热节部位添加冷铁,从而有害热节全部消除。图9为改进方案二铸件缩孔预测的结果,图中可以看出:与方案一相比在型腔壁处形成的热节基本上都已消失,冒口根部的热节移向补贴中,椭圆形冒口根部的热节也上移,所以这些热节的存在并不影响铸件的质量。
3.3、生产验证
按照原铸造工艺和改进后的铸造工艺进行生产验证,将阀体纵向切开,得到阀体型腔壁处局部缩孔、气孔的宏观形貌,如图10所示。可以看出,工艺改进后实际生产结果与模拟结果相吻合。改进后生产的铸件在模拟中显示的有害热节处所产生缩松或缩气孔缺陷得到了有效的消除。
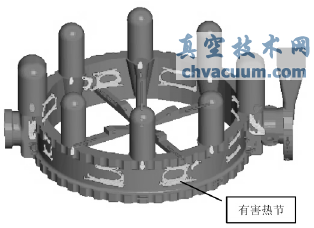
图8 优化方案一铸件热节分布图
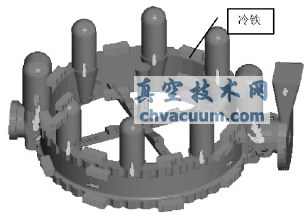
图9 优化方案二铸件热节分布图
4、结论
(1)原方案中铸件采用传统中注式浇注系统充型过程平稳,各个内浇口的钢水流速基本一致,没有出现喷射状充型,也没有产生紊流、卷气的现象。铸件没有顺序凝固,在型腔壁处产生了大量的热节,这些热节处遇到侵入性气体很有可能会产生缩孔缺陷。
(2)通过在冒口下方增加补贴,模拟分析显示充型结束后铸件各部位温差比较小,顺序凝固得到了加强,型腔壁处产生的热节比原来大大减少,但仍没有消除。通过在局部热节处添加冷铁,顺序凝固极其强烈,型腔壁处产生的热节基本上消除,缩孔缺陷亦消除。
(3)生产实验结果与模拟结果基本相同,所以通过三个模拟方案的分析优化了铸造工艺,为铸件在浇注温度、外界环境等比较理想的状态下的铸造生产提供了一定的依据。
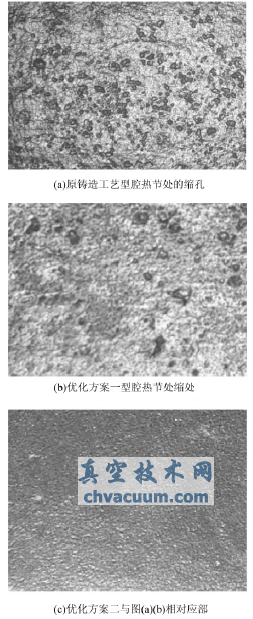
图10 铸件型腔处缩孔分布图